The balance in the design of aerospace components comes with aiming to lighten the component mass while withstanding the high structural loads on the materials. This high load-to-material strength ratio makes the components susceptible to thermal and pressure cycle fatigue, as well as vibration, due to the wide ranges of operating conditions. Additionally, corrosion from humidity in the ground air that condenses on the plane attacks the material as well.
Over 80% of inspections are performed visually by trained inspectors. Inspectors use NDT for much of the remaining 20% they cannot access visually. Initial manufacturing process and repair also use NDT. Two of the most significant NDT methods used in aerospace are Magnetic Particle Inspection (MT) and Fluorescent Penetrant Dye (PT).
Magnetic Particle Inspection (MT) Continuous Wet Bench
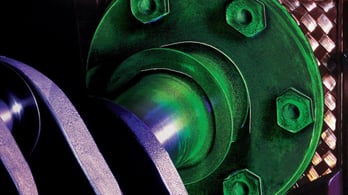
The magnetic testing (MT) method induces a magnetic field created with either AC or DC current into ferromagnetic materials (alloyed nickel and iron, among others) and partially magnetic stainless steels. The aerospace industry typically uses de-aromatized kerosene as the carrier fluid for approved wet magnetic particles. The industry mandates using a Gauss meter to determine magnetic field strength, which must be between 30-60 gauss for aerospace applications. This range enables detection of local field pattern distortion caused by discontinuities.
MT can locate cracks, seams, discontinuities, and impurity inclusions at the surface of and within ferromagnetic materials, making it a good candidate for incoming/final inspection and periodic maintenance. Due to the range in types of those potential failure points, the choice of current can improve detection. DC-generated fields penetrate the material cross-section, making it a better choice for gaps within the material. AC fields detect material gaps at the surface.
Fluorescent Penetrant Dye Inspection (PT)
Fluorescent dye penetrant inspection, or penetrant testing (PT), is another method of NDT used in the aerospace industry. One of the oldest approaches to detect surface flaws like cracks, porosity, gouges, and seams, inspectors add the dye to target areas on a surface. By capillary action, the dye finds its way into openings, coating the flawed areas. After the excess dye is removed, an additive called the “developer” is introduced, and it draws the remaining dye out. After a final cleaning step, the dye that penetrated through the developer exposes the critical cracks and porosity in the part when viewed under a black light.
While PT can be used in nearly any NDT application, compatibility of test materials must be considered for the specific industry. With the inherent severity of chemical incompatibility in the aerospace industry, manufacturers developed classes of penetrants best suited for that industry. The most common penetrant systems in aerospace are Type I (fluorescent), Methods A, B, and D (water washable, post emulsified – lipophilic, and post emulsified – hydrophilic, respectively).
Summary
Though industry examiners perform a high percentage of visual inspections in aerospace, NDT is a critical method to address the remaining fraction. Magnetic Particle and Dye Penetrant inspection are two of the most widely used techniques to assess flaws without damaging expensive parts in the industry’s broad range of applications.
Superior Joining Technologies, Inc. provides NADCAP-accredited services for both magnetic particle inspection and fluorescent dye penetrant inspection non-destructive testing services. Other competencies include gas tungsten arc welding (GTAW/TIG), laser beam welding (LBW), and resistance welding; in addition to laser cutting, laser marking processes, and additive manufacturing capabilities. SJTI is certified in ISO 9001:2015, has earned a second NADCAP-accreditation for fusion/laser welding, is listed as an FAA Repair Station OP Spec for welding and fluorescent dye penetrant and magnetic particle inspection, and is UTC Aerospace Approved to AWS.